# How Does a Trunnion Ball Valve Truly Work?
High-pressure systems causing valve failures and leaks? This creates huge safety risks and costly downtime. The trunnion valve’s…
High-pressure systems causing valve failures and leaks? This creates huge safety risks and costly downtime. The trunnion valve’s mechanical design elegantly masters these intense forces.
A trunnion ball valve works by using a trunnion to anchor the ball. Instead of pressure pushing the ball, it pushes floating, spring-loaded seats against the stationary ball. This fundamental difference creates a superior seal with significantly lower operating force, mastering high pressure.
I always tell designers like Jacky to picture this shift in thinking. A floating valve is like using a big hammer (the ball) to hit a nail (the seat). The force comes from the hammer’s movement. A trunnion valve is like a hydraulic clamp (the seats) gripping a fixed steel plate (the ball). The pressure itself provides the clamping force. This changes everything about the valve’s performance, from its durability to the cost of operating it. Once you grasp this core concept, all the other benefits fall into place. Let’s break down exactly how this mechanical genius works.
How Does its Internal Structure Tame High Pressure?
Struggling to visualize how a valve can just ignore massive pressure? You might think it needs brute strength. The magic isn’t complicated; it’s about cleverly redirecting force.
The internal structure tames high pressure by fixing the ball with a trunnion. This transfers the immense pushing force from line pressure directly into the valve body. This leaves the independent seats free to be pushed against the stationary ball by that same pressure, creating a perfect, self-tightening seal.
The most important thing to understand is this reversal of roles. In a standard floating ball valve, pressure acts on the ball. In a trunnion ball valve, pressure acts on the seats. The trunnion itself is a short, strong shaft at the bottom of the ball that sits in a bearing in the valve body, while the stem supports it from the top. These two points anchor the ball. The line pressure wants to push the ball downstream, but the trunnion and stem hold it firm, so all that force is absorbed by the valve’s metal body. Now, that same line pressure can get behind the floating valve seats and push them onto the ball’s surface. The higher the pressure, the harder the seats get pushed, and the tighter the seal becomes. It’s an incredibly smart design.
The Force Transfer Path
Component | In a Floating Valve… | In a Trunnion Valve… |
---|---|---|
Line Pressure | Pushes the entire ball downstream. | Pushes the valve seats toward the ball. |
Ball | Moves and presses into the seat. | Stays fixed, only rotates. |
Trunnion | Does not exist. | Absorbs the main force into the valve body. |
Why Doesn’t the Ball Shift Under High Pressure Like in a Floating Valve?
In a floating valve, the ball gets jammed downstream. You would expect the same to happen here. But a small component makes all the difference, preventing this movement entirely and ensuring reliability.
The ball doesn’t shift because it is mechanically anchored. The stem holds it from the top, and the trunnion holds it from the bottom. These supports act as bearings, locking the ball’s position while allowing it to rotate. All sideways force from pressure is absorbed by these anchors.
The trunnion isn’t just a simple pin; it is a critical load-bearing component. It is essentially a sleeve bearing that has to withstand huge radial forces. When selecting a valve, especially for dirty or abrasive service, this is a major point of concern for me. I’ve seen this firsthand where fine particles in the fluid get into the small space around the trunnion. Over time, these particles act like sandpaper, grinding away at the trunnion bearing. Once the bearing wears down, the ball’s center can drop, even by a fraction of a millimeter. This slight shift destroys the perfect alignment between the ball and the seats. Suddenly, the valve will start leaking, and it is a type of failure that usually requires a full factory repair. This is a critical detail for any designer working with less-than-perfect media.
The Trunnion as a Bearing
- Function: It is a sliding bearing that absorbs massive force.
- Materials: Often made of durable, low-friction materials like PTFE composites.
- Vulnerability: Abrasive particles in the media can cause premature wear.
- Failure Mode: Wear leads to ball sag, misalignment, and catastrophic sealing failure.
How Do Spring-Loaded Seats Ensure a Zero-Leak Seal at Both Low and High Pressures?
You need a perfect seal from 0 PSI to 3000 PSI. How can one mechanism work across such a variance? The secret is a brilliant two-stage system working in harmony.
They use a two-stage process. At low pressure, internal springs provide the initial force, pushing seats against the ball for a tight seal. At high pressure, line pressure acts behind the seats, creating a powerful, self-energized seal that gets stronger as pressure increases.
This two-stage system is the key to the valve’s reliability. First, the springs provide a constant, light push. This pre-loads the seats against the ball, ensuring a dependable seal even when the system is not pressurized. However, I’ve seen projects where costs were cut by using cheap springs. In corrosive service, these springs fail quickly, leading to low-pressure leaks that are hard to diagnose. We call it “weeping.” Second, the pressure-energized effect. The valve seat is designed like a piston. The area behind the seat that pressure acts on is larger than the sealing face against the ball. This pressure difference creates a massive net force pushing the seat even harder onto the ball as system pressure builds. The magic here is the O-ring on the seat, which acts like a piston ring, allowing pressure to build behind the seat. If that O-ring fails from aging or chemical attack, high-pressure sealing is lost instantly.
How Does the Trunnion Support Lower Operating Torque by Over 70%?
High torque means you need a bigger, more expensive actuator. This increases the valve’s cost and footprint. So how does the trunnion design slash this requirement so dramatically?
The trunnion design cuts operating torque because the actuator only needs to overcome friction. It does not have to fight the massive force from line pressure, which is entirely absorbed by the trunnion anchor and valve body.
Think back to my hammer and clamp analogy. In a floating ball valve, turning the stem is like trying to twist a hammer while someone is pushing it sideways with incredible force. You are fighting both friction and the entire line pressure load. With a trunnion valve, that sideways force is gone. The pressure load is handled by the static trunnion bearing. All the actuator has to do is rotate the “fixed steel plate” inside the “hydraulic clamp.” The only resistance is the friction from the seats pressing against the ball and the friction in the stem and trunnion bearings. The difference is enormous. I’ve helped clients reduce their actuator size and cost by more than half just by switching from a large floating valve to a trunnion design for the same high-pressure application. This is a direct, measurable cost saving that designers like Jacky can build right into their plans.
How Does the “Double Block and Bleed” (DBB) Feature Mechanically Ensure Safety?
“Double Block and Bleed” sounds like a complex feature. But its function is simple: create a provably safe barrier for maintenance. How do the valve’s mechanics make this possible?
DBB works because the valve has two independent, spring-loaded seats. When closed, the upstream seat and the downstream seat both seal against the ball. This isolates the central valve cavity, which can then be bled off and verified as zero-pressure through a bleed valve.
The DBB feature is a direct result of the pressure-energized, independent seat design we already discussed. Because the ball is fixed, each seat can act as its own standalone barrier. When you close the valve, the upstream pressure pushes the upstream seat against the ball, creating the first “block.” At the same time, the downstream seat is also pressed against the ball by its spring, creating the second “block.” The space between these two sealed seats—the valve’s body cavity—is now completely isolated. A technician can then open a small bleed valve on the side of the valve body to safely release any trapped fluid or pressure from this cavity. This is critical for safety. It allows maintenance crews to physically verify that the valve is providing a true double-barrier seal before they start working on the downstream pipe.
What Are Self-Relieving Seats and How Do They Prevent Overpressure?
Trapped liquid can heat up and expand. This can cause dangerous overpressure inside the valve. How does the valve handle this automatically?
Self-relieving seats are a safety design where excess pressure inside the valve cavity can automatically push a seat slightly away from the ball. This allows the overpressure to safely vent into the pipeline, preventing a dangerous pressure buildup within the valve body.
This is another brilliant aspect of the “seat-as-a-piston” design, often called a Single Piston Effect (SPE) seat. Normally, line pressure is higher than cavity pressure, so it pushes the seat against the ball. But if a trapped liquid in the cavity heats up, the cavity pressure can become much higher than the line pressure. In this situation, the force from the cavity pressure acting on the back of the seat becomes stronger than the force from the line pressure and the spring combined. This net force pushes the seat away from the ball, opening a tiny path for the excess pressure to escape into the main line. Once the cavity pressure drops back to normal, the line pressure and spring take over again and the seat re-seals against the ball. It’s a simple, passive safety feature that prevents the valve from becoming a pressure bomb.
What’s Special About the Stem Sealing Design to Prevent Leaks?
The stem is a common leak path in any valve. In a high-pressure valve, a stem leak is a major failure. Trunnion valves use multiple layers of protection to prevent this.
Trunnion valve stems often feature a double or triple sealing system. This includes primary and secondary O-ring seals, plus backing rings to prevent extrusion, and often a final layer of graphite packing for fire-safe designs, ensuring maximum containment.
Because trunnion valves are built for high-pressure, high-consequence service, the stem sealing area is seriously over-engineered. It’s not just one O-ring. A typical design has multiple layers of defense. There is usually a primary O-ring for the main seal, then a secondary O-ring for redundancy. Crucially, especially for high pressures, these O-rings are supported by anti-extrusion rings. These hard plastic rings sit behind the O-rings and prevent the high pressure from squeezing the soft elastomer out of its groove. For services that require a fire-safe rating, there is another layer of graphite packing. If a fire were to burn away the plastic seals, the graphite would expand with the heat and form a durable seal, preventing flammable fluid from escaping. Some designs even include an emergency grease injection port to temporarily seal a damaged stem packing.
Now That You Understand the Principles, How Do You Choose the Right Configuration?
You understand the theory, but how do you turn that into a spec sheet? Making the wrong choice can negate all the advantages. A systematic approach ensures you get the performance you need.
To choose the right configuration, you must match the valve’s components—seats, seals, springs, and materials—to your specific service conditions. Prioritize pressure, temperature, fluid type, and required safety functions like DBB or SPE.
As a designer, Jacky would need to go through a checklist. It’s what I do with every client to make sure we don’t miss anything. You need to think systematically about the application from the inside out. Start with the fluid—is it corrosive or clean? This dictates your material choices for the body, ball, and especially the springs. Then, look at the pressure and temperature range, as this will determine the type of seat and seal materials you need (e.g., PTFE vs. PEEK for seats, Viton vs. HNBR for O-rings). Finally, consider the operational requirements. Do you need DBB for maintenance safety? Do you need self-relieving seats? Answering these questions builds your final specification.
Your Configuration Checklist
If Your Project Has… | You Need to Specify… | My Insider Tip |
---|---|---|
Abrasive or dirty media | Hard-coated ball (e.g., Tungsten Carbide) and protected trunnion bearings. | Don’t overlook the trunnion bearing; this is where gritty fluids will kill a standard valve. |
Low-pressure gas | High-quality springs (e.g., Inconel) to prevent “weeping.” | This is the most common failure point for low-pressure sealing. Don’t cut costs on springs. |
High temperatures | Polymer seats like PEEK and robust elastomers like Viton® or AFLAS®. | Always check the full temperature range, including potential upset conditions, not just normal operation. |
Critical safety requirements | Double Block and Bleed (DBB) or Double Piston Effect (DPE) seats. | Understand the difference: DBB with SPE seats is standard; DPE locks pressure in the cavity. |
Conclusion
A trunnion valve masters high pressure with its fixed ball and pressure-activated seats. Understanding these core mechanics is the key to selecting the right, reliable configuration for your project.
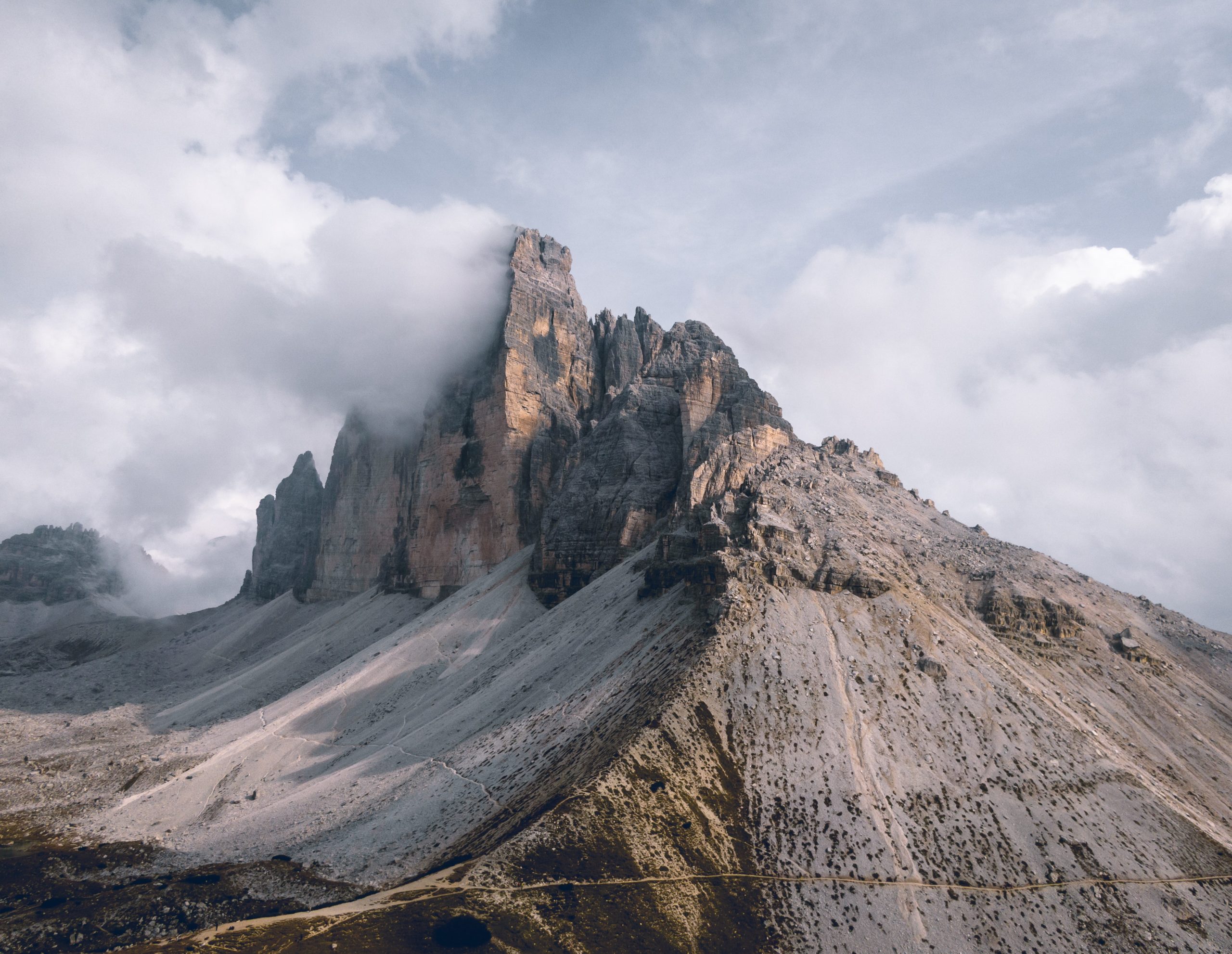
Give your list item a title
Give your list item a title
Tell your story in numbers, and give your visitors useful insights.
Make an impact, and share your organization’s stats or achievements to interest your website visitors into learning more about you.
Stat title
Stat title
Stat title
Stat title
Stat title
Stat title
Stat title
Add an overline
Add a short & sweet headline
Craft a captivating title for this section to attract your audience.